|
Source: IABU System Integration
Efficiency of System Integration:
In the general and traditional control system, because of the place where the temperature controller is installed or the largest capacity design on the system, the fan runs in fixed frequency. Thus, when the ambient temperature reaches the set temperature, there will still be too much cool air, resulting in the waste of energy. The temperature that is too low also makes the people in the environment feel uncomfortable. However, with Deltaˇ¦s human machine interface and temperature controller, you are able to control the temperature of your working environment. The handy interface allows you to set up your desired temperature precisely (to one digit after the decimal point), and by the PID operation in the temperature controller, you can modulate the openness of the valve as well as the wind volume, which not only helps maintain the constant temperature, but also reduces the consumption of chilled water and power for the water chiller. Therefore, with only very little expenditure on the materials and construction, you can work or live in a comfortable environment and save energy every day!
System Reform:
In theory, half of the motor running speed (reducing from 60Hz to 30Hz) requires only 1/8 of the energy. However, due to the CO2 exhaled from the people in the environment, in experience, a normal air circulation requires the running speed of the motor at least at 30Hz.
The openness of the chilled water valve can modulate the volume of chilled water. If there are many water chillers in the system, you can also decide whether to remove some chillers by the PLC program in reducing the waste of energy.
Use Delta's Product in Your Equipment:
|
Model |
Parameter Setting |
HMI |
3.8 inch |
For all series. 3.8 inch model is the most economical one. |
AC Motor Drive |
F or E series |
1. |
The frequency is controlled by RS-485 communication. |
2. |
The operation is controlled by RS-485 communication and Stop key. |
3. |
Communication format: 9600, 7, E, 1. |
|
Temperature Controller |
DTC1000L |
1. |
Cooling control |
2. |
PID control (P=1, I=240, D=0) |
|
Program Operation:
We do not use PLC in this system but the macro commands in the HMI to display the program in a simple way. See below for the screen and the compilation of macro. AC motor drive is at ID#1, and temperature controller at ID#3.
ˇ˝ HMI Display:
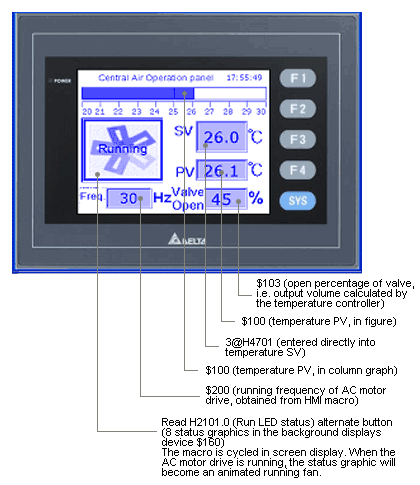
ˇ˝ Macro Program:
The macro consists of three parts: clock, button on/off and cycle.
Clock Macro: Calculating the frequency and write the value into the AC motor drive.
01. |
Comment |
02. |
Read the temperature controller H1000 (PV) and put it into $100 for display. |
03. |
Read the temperature controller H1012 (output volume) and put it into $102. |
04. |
The output volume $102 is to one decimal place, so divide the value by 10 and extract the integer result and store it in $103 for display. |
05. |
Comment |
06. |
When the output volume $102 of the temperature controller is less than 60.0%, jump to LABEL 1 and set $150 as 3,000 (i.e. the frequency of AC motor drive as 30.00Hz). Use this row to maintain the lowest speed of the AC motor drive at 30Hz. |
07. |
When the output volume $102 of the temperature controller is larger than 60.0%, send output volume*5 to $150. (When the output volume is between 60% ~ 100% , the frequency has to be between 30 ~ 50Hz.) |
08. |
Jump to row 11 |
09. |
LABEL 1 |
10. |
When the output volume $102 of the temperature controller is less than 60.0%, fix the frequency $150 of the AC motor drive at 30.00Hz. |
11. |
LABEL 2 |
12. |
Send the frequency $150 calculated by the macro to the register in AC motor drive H2001. |
13. |
The frequency $150 is a two decimal digit, so divide the value by 100 and extract the integer result and store it in $200 for display. |
Button On/Off Macro: Stop/Run the AC motor drive
01. |
The button is alternate. When the button is ON, enable "editing ON macro" and set H2000 in the AC motor drive as "2" to run the AC motor drive.
|
02. |
When the button is OFF, enable "editing OFF macro" and set H2000 in the AC motor drive as "1" to stop the AC motor drive. |
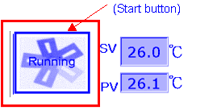
Cycle Macro: Animating the running of fan when the AC motor drive is in Run status
1. |
Read H2101.0 (Run LED status) of the AC motor drive. When Run LED is On, the 8 animated status graphics of the fan start to change. |
2. |
Move to row 9. |
3. |
LABEL 1 |
4. |
When the 8 th graphic is displayed, jump to LABEL 10 and make $160=0 to switch back to the first graphic. |
5. |
Plus "1" to the value in $160 to display the next graphic. |
6. |
Move to row 9. |
7. |
LABEL 10 |
8. |
When the 8 th graphic is displayed, the program will jump to this row and make $160=0 to switch back to the first graphic. |
9. |
LABEL 2
|
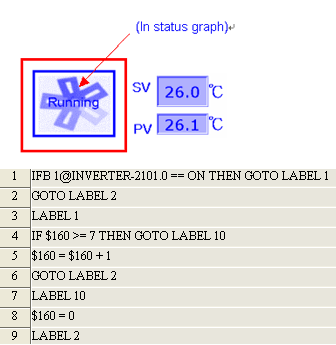
|
|